Process Enhancement
Quality is never an accident. It is always the result of intelligent effort – John Ruskin
In the most productive and quality driven environments process enhancement (CI) is constant and part of the fabric. Once we genuinely understand what we are doing and why we are doing it we can then start to look at how we are doing it. There may be substantial changes but usually, for established processes, it is the aggregation of marginal gains (Kaizen).
CCM will look, not to use repeat visits for single issues, but establish a continuous improvement culture in organisations that supports constant change for the development of quality and productivity.
Process Enhancement
Quality is never an accident. It is always the result of intelligent effort – John Ruskin
In the most productive and quality driven environments process enhancement (CI) is constant and part of the fabric. Once we genuinely understand what we are doing and why we are doing it we can then start to look at how we are doing it. There may be substantial changes but usually, for established processes, it is the aggregation of marginal gains (Kaizen).
CCM will look, not to use repeat visits for single issues, but establish a continuous improvement culture in organisations that supports constant change for the development of quality and productivity.
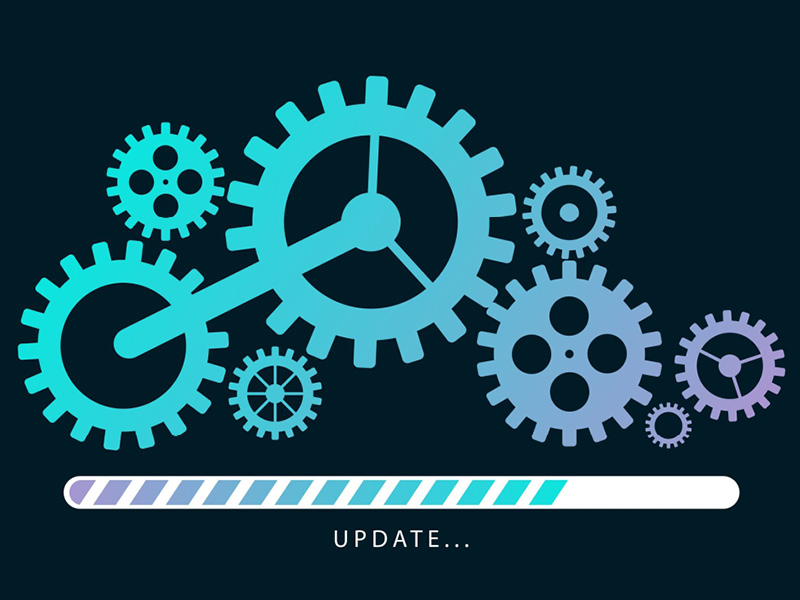
Process Enhancement
Productivity
All outputs, both soft and hard are productivity. Improving productivity is inextricably linked to profit in business. When we increase our output, this should not be at the cost of quality. Planning, research, shadow testing and operator engagement are all key to successful and quality driven productivity improvements.
Process Enhancement
Lean Tools
Lean tools, used properly, can boost productivity and profitability, while transforming the work environment. Discipline is required and all colleagues will need to be engaged to the process. Once a Lean environment is established continuous improvement will be a natural by-product of the working group, flow will increase, errors reduce.
Measure twice, cut once.
Process Enhancement
Value Stream Mapping
Understanding the processes is key to reducing wastes and improving process flow. Value stream mapping looks at each step of the process and identifies which are value add and which are non-value add – one of the 7 wastes.
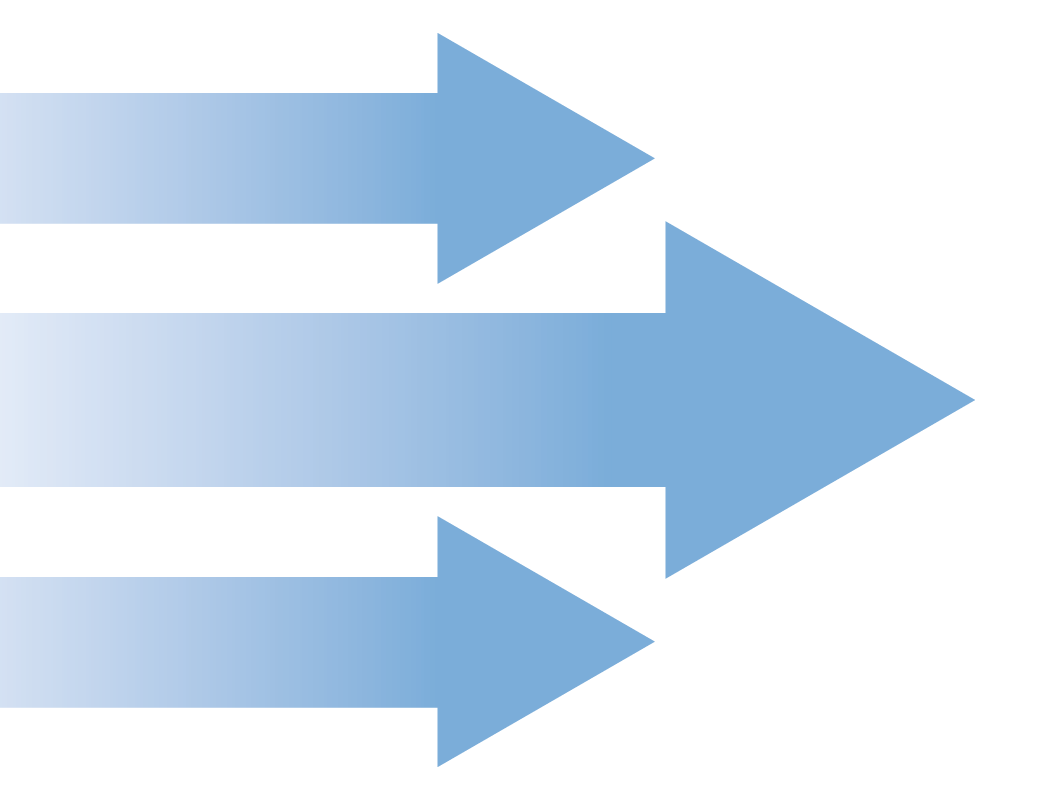
Process Enhancement
Root Cause Analysis
Essential to any continuous improvement process is a thorough root cause analysis programme – CI. There are many forms of root cause analysis which can be adapted for each situation. Most important, for these tools to give us progressive information, is that they are used in a consistent, independent, and non-judgemental way. The method should provide a corrective action (containment) and solution (new procedure).